
Automatic hot air energy-saving reflow soldering machine
- Transportation:
- Ocean
- Port:
- Yantian Port, Shenzhen
Your message must be between 20 to 2000 characters
Contact NowPlace of Origin: | China |
---|---|
Productivity: | 300 units/year |
Supply Ability: | Sufficient supply |
HS Code: | 8515190010 |
Transportation: | Ocean |
Port: | Yantian Port, Shenzhen |
Automatic hot air energy-saving reflow soldering machine
With the development of many electronic products in the direction of small, light, and high-density, especially the large-scale use of handheld devices, the original SMT technology has been severely challenged in terms of component materials and technology, and SM has been developed rapidly. Chance. The IC pin pitch has developed to 0.5mm, 0.4mm, and 0.3mm. BGA has been widely adopted, and CSP has also emerged and is showing a rapid upward trend. The materials are widely used for no-clean, low-residue solder paste. All of these have put forward new requirements for the reflow soldering process. A general trend is to require reflow soldering to adopt more advanced heat transfer methods to achieve energy saving, uniform temperature, and suitable for the soldering requirements of double-sided PCB and new device packaging methods. Gradually realize the comprehensive replacement of wave soldering. Generally speaking, the reflow oven is developing in the direction of high efficiency, multi-function and intelligence. There are mainly the following development paths. In these development areas, reflow soldering leads the development direction of future electronic products.
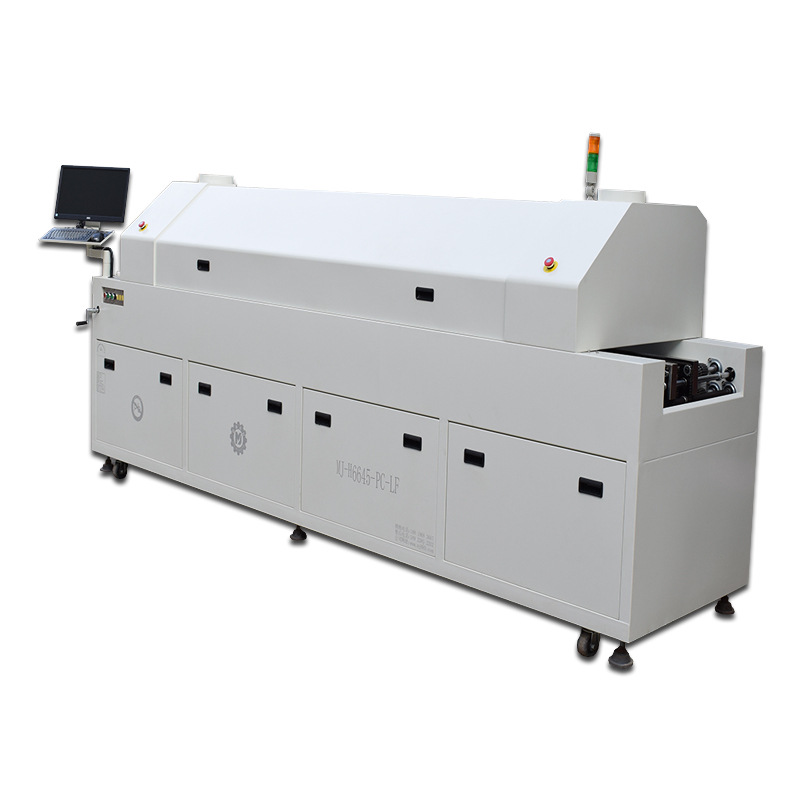
Product features
1. With temperature tolerance, fault diagnosis, sound and light alarm functions.
2. Modular design of the heating zone, convenient maintenance and disassembly, independent small circulation air transport design, upper and lower heating methods, good thermal compensation, high thermal efficiency, power saving, plus
Fast temperature speed, suitable for welding of high-quality products such as BGA and CSP components, special forced hot air circulation structure system, so that PCB and components are heated evenly and efficiently
High and fast heating speed.
3. The air transport system adopts advanced air duct design, uniform air transport and high heat exchange efficiency.
4. The preheating zone, welding zone and cooling zone are heated independently up and down, cycled and temperature controlled independently. The temperature difference between adjacent temperature zones can reach up to 100℃.
The temperature and wind speed of the zone can be adjusted independently.
5. The power of each temperature zone is properly matched, and the temperature rises quickly, from room temperature to set working temperature about 15 minutes. And has fast and efficient thermal compensation performance.
6. Modular design, compact structure, convenient maintenance.
7. With independent roller structure and topping support, combined with stainless steel mesh belt, it runs smoothly and is durable and wear-resistant. Long-term use is not easy to change.
Installation and use conditions
<1>Working voltage: AC380V±10%; three-phase five-wire system; 50Hz, can also be connected to 220V.
<2> Ambient temperature: 5~40℃;
<3>Relative humidity: not more than 85%RH;
<4>Power switch: air switch
<5>Installed power: 18KW
<6>The ground is flat, and there should be no strong vibration and corrosive gas in the surrounding environment.
Reflow soldering process
Printed board preparation-solder paste preparation-printing solder paste-mounting post-chip components-through reflow soldering-soldering completion-testing-shaping and trimming-completion
Company strength
Workshop shots
Item display
About delivery
All the equipment of the company includes freight and distribution fees, excluding the cost of going upstairs, depending on the distance, choose logistics consignment or door-to-door delivery
On-site installation and commissioning
The company is responsible for distribution, and there are professional engineers on-site installation, commissioning, training, or guidance and assistance through remote video or telephone
1 year warranty
After-sales promises that all parts of the wave soldering machine are guaranteed for one year, except for human problems
Lifetime service
The company provides life-long maintenance, paid service, only labor costs and material costs
Preparation before installation and commissioning
1. Door-to-door time: within 2 working days after all the following work is ready, special circumstances will be discussed separately
2. Logistics transportation: After receiving the goods, customers who choose logistics transportation must first place the equipment and prepare all the following materials
3. Home delivery: Customers who choose home delivery need to reserve space in advance to prevent equipment and prepare all the following materials
Material preparation:
1. Power connection: lead the power cord to the device according to the requirements of the device, leaving a length of more than 3 meters to connect to the device
2. Air connection: If there is an air source in the workshop, lead the air pipe to the side of the equipment, leaving a length of more than 3 meters to connect to the equipment. If there is no air source in the workshop, you need to prepare the air compressor in advance and prepare the necessary accessories
3. Tin bar: Prepare enough tin bars in advance according to the tin capacity requirements of the equipment, so that the master can directly melt the tin for on-site trial welding test and training when he comes to the door.
4. Flux: the flux that needs to be used when the product is ready for trial welding. At least 2 liters required for testing
5. Cleaning agent: the nozzle used to clean the flux, temporarily not used, it will not affect the debugging
Related Keywords